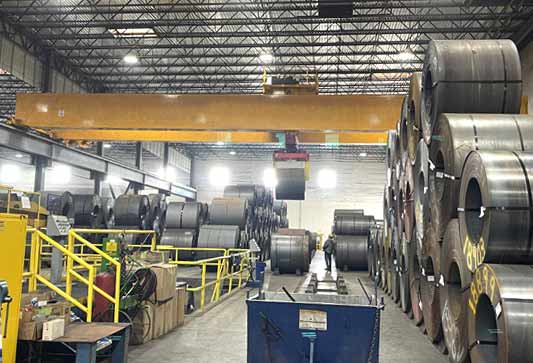
PRIMARY METALS PROCESSING
AND STORAGE
Ace Industries offers a wide variety of hoist and bridge crane options to provide the best products for our metals and steel warehousing customers. Plate handling, coil handling, multiple profile beams, rebar, structural steel and tubing operations are specialized applications that require unique lifting solutions and below-the-hook devices such as magnets or hydraulic grabbers to carry loads efficiently, reliably, and safely even in the harshest, high temperature working environments.
Our customer's casting, storage, feeding, and forging crane production processes dictate the hoist and equipment manufacturer we provide. When it comes to brands, Ace carries the best quality with reliable factory supported backing. Uniquely, Ace does not depend on our customers to purchase specific OEM brands to make a profit. We make brand recommendations with the goal of tailoring the right brand and product to the specific application. We know that the marketplace is competitive, and reliability and efficiency is necessary to meet today’s industry demands.
THE METALS AND DISTRIBUTION INDUSTRY
IS A 365 DAY A WEEK BUSINESS, AND WE ARE
ON CALL TO MEET ANY NEEDS THAT MAY
ARISE DAY OR NIGHT.
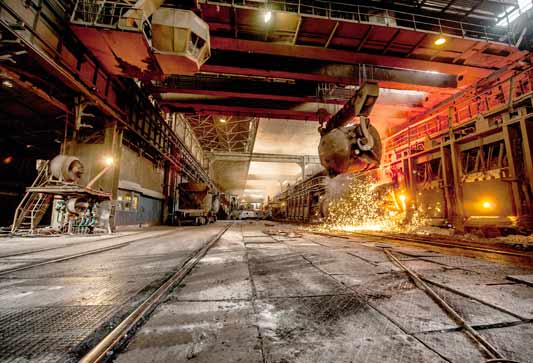
The metals and distribution industry is a 365 day a week business, and we are on call to meet any needs that may arise day or night. Our technicians are knowledgeable about steel industry cranes and can quickly diagnose and repair most issues without requiring additional specialists or technical support. At Ace, we provide the correct equipment and the right service program to meet high demands based on our metals and steel warehousing customer’s crane OEM, duty class and usage. Trust and transparency are vital to any relationship. Ace offers equipment and asset analytics which produce up-to-date tracking of spending to the asset level, via our customer portal.
Schedule a consultation with an Ace representative. To learn more, call (800) 733-2231 or email us at sales@aceindustries.com.
“WE RELY ON ACE. NOT JUST RELY ON THEM, WE LEAN ON THEM. WE WANT THEM AS A RESOURCE.
THE RELIABILITY OF OUR CRANE OPERATING SYSTEMS HAS IMPROVED WITH ACE’S HELP. IT BOILS DOWN
TO THIS: HONESTY, INTEGRITY, TECHNICAL KNOWLEDGE, AND BOOTS ON THE GROUND SKILL
AT A FAIR PRICE. THEY HAVE REPRESENTED ALL THIS FROM DAY ONE.”
—D.L., STEEL MANUFACTURING
FACILITIES & MAINTENANCE MANAGER
METAL PROCESSING CASE STUDY
Process Crane End Truck Replacement
Overhead cranes are an integral part of steel distribution. In 2011, a steel manufacturing customer broke ground on a new mass distribution center in Vancouver, Washington, consolidating production from sites around the Pacific Northwest. Each previous location specialized in a specific type of steel, such as rebar or plate. The steel product, typically heavy, in various weights, shapes, and sizes, has to be moved from one end of the facility out the door and onto a truck that ships it to customers. Alongside Class D and Class C standard duty types of cranes used for support activities, the customer had nine Class E specialized workhorse cranes needed for continuous production. These massive overhead cranes are big and very fast. Each crane has a rotating trolley that spins around to move plate steel product 90 degrees, which is easier for the operator and helps with placement from the production line onto trucks.
During the commissioning process of the Class E cranes, and after start up, there were several problems. The customer had issues with premature wear on the drum due to incorrect rope construction, problems with the bridge, and drive torque arm assemblies snapping off. It's not typical to have these types of problems on a brand new crane. The majority of the issues were around the Class E specialized cranes. In time most of the issues were addressed, however, there was an ongoing problem with the bridge drive assembly that was never resolved. This was due to the under-sizing of the bridge drive assembles and wheel bearing. These cranes travel at speeds of 270 feet per minute. In the crane world, that's pretty fast! The end trucks, and 12” wheels on these cranes appeared to be undersized, and as a result, the customer was experiencing bridge failures every 18 months or so. Note that a typical bridge bearing could last 20 years. First it was bridge wheel bearing failures then there were related issues involving the gearbox, like a domino effect creating the perfect storm for a breakdown.
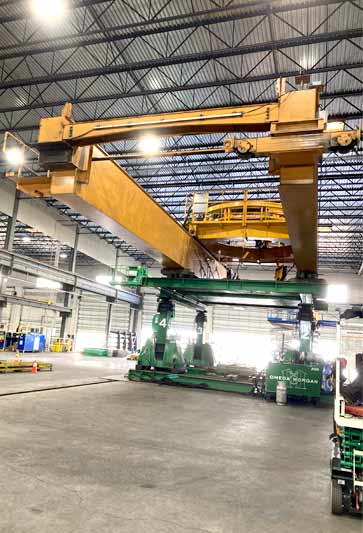
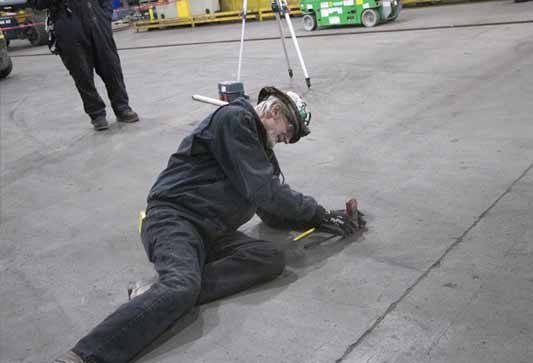
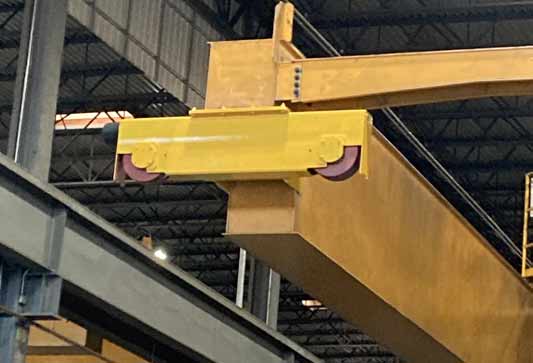
Since the repairs required to fix this condition were complicated and would have to involve a machine shop, it would require multiple days of costly downtime. Every time the customer had a bridge drive failure, they wouldn't be able to use the crane, which meant not getting their product out the door and to their customers, so it was a very expensive band-aid.
Ace determined the right solution would be to get the right size bridge drives and wheels for heavy-duty cranes. The Ace Portland, Oregon branch was fortunate enough to start servicing the account in 2017 and, at that time began performing some modifications to the bridge drives. They extended the shaft, reinforced the bridge and the wheel capsules, and some other fixes that helped. But the cranes were still continuously having failures.
In particular, the steel customer had one Class E crane that was more of a problem than the others. Each of their eight bays is reserved for a specific type of steel processing, and bay six crane, which handles steel plates, only had a single crane, thus no backup in case of a break down. Unfortunately, this crane was experiencing premature wear on the northwest drive wheel. The wheel would only last for six months to a year and then need to be replaced.
When this was discovered, Ace teamed up with a highly credentialed and world renowned professional IMS engineer, Gary Davis, and he was able to provide some intelligence on the crane's squareness and runway alignment. Gary Davis worked with our local Portland branch team to diagnose the issue. He performed a comprehensive runway survey and alignment analysis utilizing a total station survey device.
After Gary’s analysis, it was determined that the crane was not square, the runway was not in span and there were some elevation issues. Compound these issues with the undersized end truck and bridge wheel, and it was apparent that the customer had a significant problem on their hands. Ace and Davis proposed to replace the end trucks and undersized bridge wheels for a drive configuration that was foot mounted with 15” wheels, a much more appropriate design fort this type of application and duty cycle.
Our local Portland service group worked with the customer to determine proper installation areas and schedule a window of time that would work for both Ace and the customer. With a good plan in place a team of technicians would perform the end truck replacement and another team would work on straightening the rail. Gary Davis was involved with the project from the very beginning stages and was on site to oversee and direct the installation and alignment of the of the end trucks, crucial to make sure everything was fully level and fully square.
A rigging company was hired to remove this massive crane utilizing a specialized 250 ton gantry and our team worked with Davis and IMS to reconfigure new end trucks, bridge drives, and connection plates to make sure they had the right upgrades, the right wheels, and the right bridge drive configuration to ensure a 20 year service life for the bearings.
The project was a success, everything went well, on time and as scheduled. Ace load tested the crane and everything checked out. Ace started on a Saturday and by two o'clock the following Sunday, the customer was able to run their scheduled shift. The crane runs faster, smoother and quieter than before.
Disclaimer—Ace Industries protects the rights of our customers and honors their non-disclosure requests to withhold name of company and employee for case studies, direct quotes and testimonials on aceindustries.com. Initials and job titles used for identification reference only.