CRANE TYPES FROM A-Z
At Ace we like to say “the sky’s the limit” and that’s just what you’ll find when you shop for a crane with us. A consultation with an Ace representative will cover every aspect of your overhead lifting needs and facility to determine the best fit for a crane product.
What is the amount of space you’ve got to work with? How many lifts per hour or day will your crane be performing? How heavy is the load you’re lifting? How far will it travel? These questions and more will help us help you select the right type of crane for your application.
Cranes come in a variety of models that handle different kinds of production, lifting anything from car engines on an assembly line to tons of steel in a manufacturing plant to marine components in a shipyard.
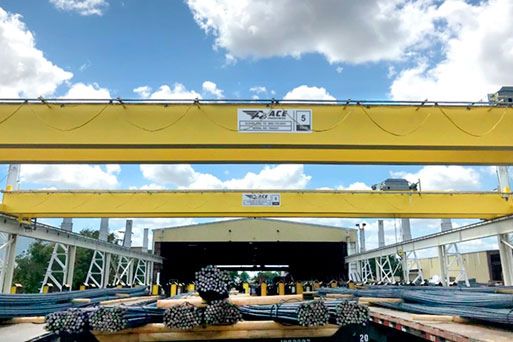
about overhead bridge cranes
An overhead crane, also known as a bridge crane, is typically found close to the ceiling in industrial environments, and is used for manufacturing, storage or maintenance applications to aid in the lifting, maneuvering, and unloading of materials. Overhead cranes can be directed by an operator either manually or with wireless controls. They tend to have low maintenance costs comparatively and offer the most lifting height for higher vertical stacking and efficient use of space and because they don’t occupy floor space, they provide better visibility for operators than forklifts.
Buyer Tips for Bridge Cranes
Choosing the lowest price crane bid without understanding the variances in equipment quoted, may result in additional long term maintenance costs to you. Selecting the proper equipment for the application is important. Prior to compiling specifications for RFQ submittal, here are some basic points to consider:
- What type of “Service” will the overhead crane be used for?
- What is the “Frequency” or how often will the bridge crane be used?
- What “Speed” of the bridge, trolley and hoist is necessary to match production efforts?
- Does the buyers’ budget match the specifications desired?
Why do minor changes in the length, width or height of a system impact the overall cost?
Steel comes in standard lengths. Beams: 30’, 40’, 50’ & 60’ angle: 20’ & 40’ tube steel: 40’ & 48’.
Adding another foot of lift or increasing the length of just one bay, could change the design and therefore, the cost.
TYPES OF OVERHEAD BRIDGE CRANES
Additional Buyer Considerations
- What are the long term maintenance costs associated with less expensive crane systems and components?
- Are replacement motors and other parts readily available from multiple suppliers or just one?
- Does the crane provider meet your company’s minimum liability insurance requirements?
- Does the crane provider adhere to all CMAA manufacturing guidelines and specifications?
- Does the crane provider have engineering and manufacturing capabilities or do they outsource these services?
- Are the replacement components readily available, to eliminate potential long lead times and increased costs?
- Does the crane provider have their own installation team or do they outsource installation?
- Does the crane provider have their own installation team or do they outsource installation?
- Not having a qualified crane company install the runway? Make sure the runway is installed to meet the CMAA runway tolerance specifications. An improperly installed runway will either delay installation of the bridge crane or create future problems and add additional costs.
- Are you considering whether or not you will be able to increase the capacity of the crane or add a 2nd bridge in the future? If so, verify if the runway beam size and rail quoted is adequate for future upgrades.
TOP RUNNING SINGLE GIRDER CRANES
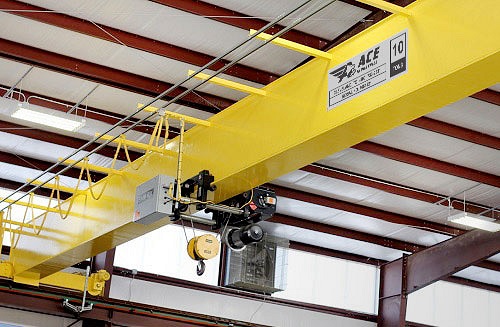
Capacity (Ton): 0.5 to 15 ton capacities |
Span: 10 to 100+ft. spans |
Key Benefit: Easy installation and service, optimal lifting height |
An overhead traveling crane that utilizes a single bridge beam attached to the two runway/end trucks that are attached to the top of the crane runways. This bridge beam or single girder supports a lifting mechanism or hoist that "runs" on the bottom flange of the bridge beam. The top running crane achieves greater lifting height compared to under running systems and installation and service are easy.
UNDER RUNNING SINGLE GIRDER CRANES
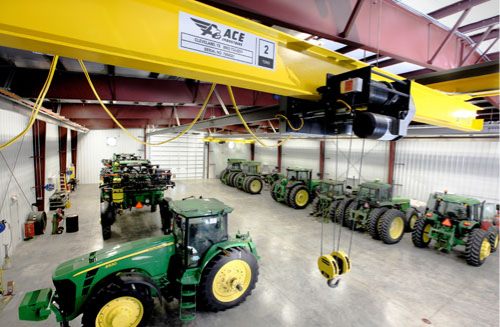
Capacity (Ton): 0.5 to 15 ton capacities |
Span: 10 to 100+ft. spans |
Key Benefit: Easy installation and service, optimal lifting height |
Under running bridge cranes are an efficient solution to free up floor space as this type of system is typically supported directly by the building roof structure and does not require columns. This type of crane is an electric overhead traveling with the end trucks supported on tracks attached to the bottom flanges of the beam; or supported on bottom flanges of beams. These beams make up the crane runway.
TOP RUNNING DOUBLE GIRDER CRANES
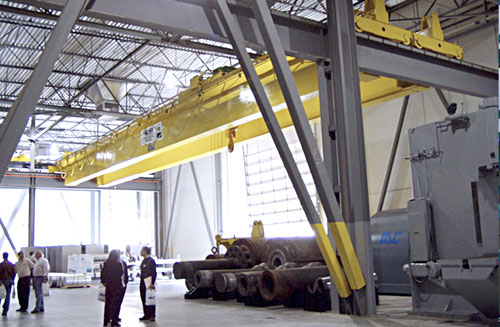
Capacity (Ton): 20 ton and greater capacities |
Span: 10 to 100+ ft. spans |
Key Benefit: Increased lifting height, greater lifting capacities, longer spans |
Typically, a top running bridge crane, a double girder system utilizes two girders as the bridge structure and a hoist trolley unit that traverses across rails mounted atop the two bridge girders. The hook from the hoist "falls" between the two bridge beams. Headroom under the crane is increased by utilizing this hoist/crane configuration. A hoist/trolley variation might configure an underhung hoist trolley unit attached to bottom of the bridge girders.
MONO AND DOUBLE BOX GIRDER CRANES
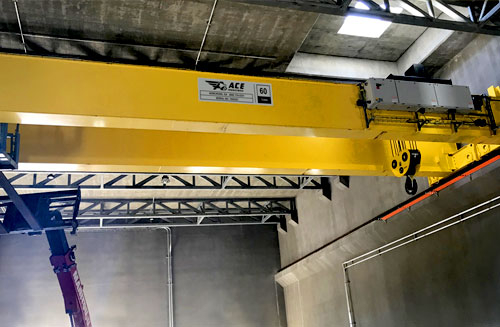
Capacity (Ton): Mono 3 to 15 tons, Double 5 tons and greater capacities |
Span: 50 to 100+ft. spans |
Key Benefit: Free-standing, space saving, highest hook height & capacity |
Instead of the typical steel I-beam make-up of the bridge, the box girder crane’s bridge is specially engineered and constructed as a hollow box. This structure can withstand more tension and rotating forces, allowing for some of the largest load capacities of all overhead cranes. A free-standing box crane provides the strength needed to lift heavy equipment without the need of columns or posts. Provides extra strength for longer spans and girder depth can be designed to improve hook height.
LIGHTWEIGHT OVERHEAD CRANES
Compact, lightweight, industrial quality overhead cranes are ideal for lifting equipment, machines and heavy parts in more confined spaces or on assembly lines for either manual or powered hand-operated applications. When you’re looking for a portable option that can be moved around your facility easily, lightweight overhead cranes might be the smartest and safest lifting solution.
LIGHTRAIL/WORKSTATION CRANES
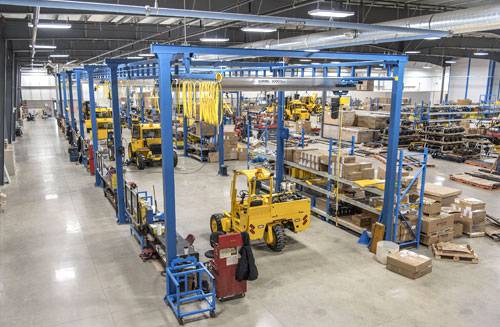
Capacity (Ton): Typical capacities up to 2 tons |
Mount: Floor supported or ceiling-mounted modular systems |
Key Benefit: Easily relocated, ideal for leased buildings, precise lifting |
Lightrail or workstation cranes are an ideal solution for light duty lifting in applications with specific work areas like manufacturing with workers positioned at stations who perform precision lifts. They consist of a moving bridge that runs across parallel runways with a hoist or other lifting device traveling its span. These systems are cost-effective and modular, allowing easy expansion and relocation as lifting needs change.
LEARN MORE
JIB CRANES
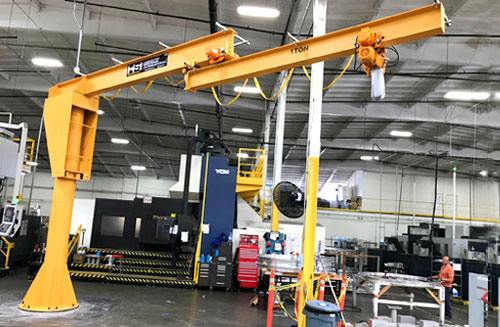
Capacity (Ton): Capacity (Ton): Up to 5 ton capacities |
Mount: Free standing or wall mounted |
Key Benefit: Maximized floor space, up to 360 degree rotation |
Jib cranes have a boom arm that supports a moving hoist and are compact, ideal for operations with limited space. Similar to workstation cranes, jib cranes provide a great application specific solution where precise load positioning is required, are simple to operate and require less maintenance than overhead cranes. The cantilevered boom lengths run up to 30’ standard with longer spans available. Jibs come in motorized and articulating options.
LEARN MORE
GANTRY CRANES
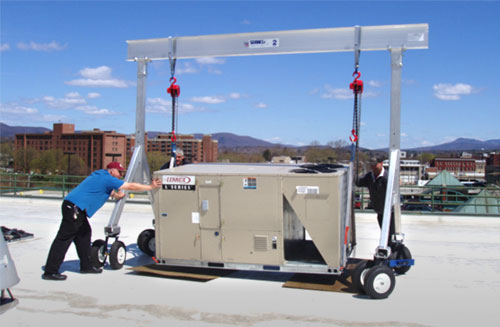
Capacity (Ton): Typical capacities up to 15 tons |
Mount: Portable or stationary options available |
Key Benefit: Can be disassembled, easily transported and re-assembled |
Gantry cranes are very versatile and can be built to your specifications no matter what size or capacity. Most motorized or higher capacity gantries, those above 5 ton and 30 foot span, are custom designed for a customer’s unique application. Gantry cranes are made light-weight, portable and adaptable for varied uses. Both fixed and adjustable heights are available.
LEARN MORE
DAVIT CRANES
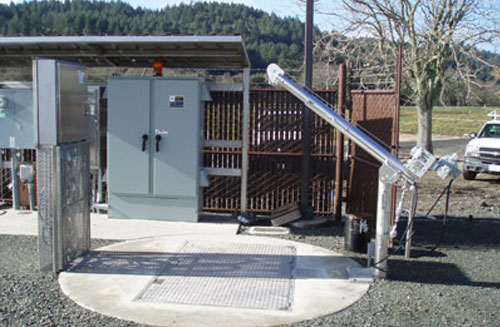
Capacity (Ton): Typical capacities up to 2200 pounds |
Mount: Portable or mounted in concrete |
Key Benefit: Installation requires less labor and is less material intensive |
A Davit crane consists of an angled beam which pivots over a vertical axis. They are a light duty, versatile, lifting system typically used in applications where lifting from an elevated position is required (e.g. lifting an object from below an elevated platform or from within a pit). Davits come in manual or motorized options and have fixed or adjustable lengths.
LEARN MORE
CUSTOM DESIGNED CRANES AND LIFTING APPARATUSES
Ace Industries employs a full in-house, quality-driven team of engineers who routinely create innovative solutions for a variety of difficult, application specific problems for our customers. If standard crane systems don’t resolve your equipment needs, our skilled and seasoned engineers can take your specifications and design a fully customized, site specific, workable solution for your facility from the ground up, taking into account any architectural obstacles or existing equipment to work around.
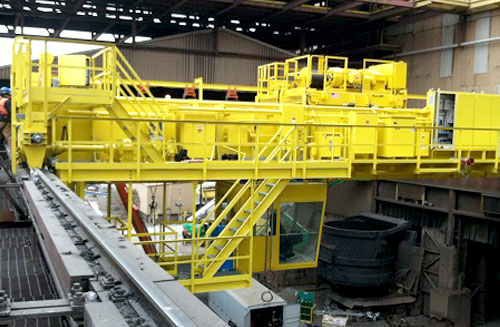
Capacity (Ton): Custom engineered/application specific |
Environments: Standard or hazardous location applications |
Key Benefit: Unique custom crane systems/below the hook apparatuses |
Ace engineers specialize in systems design. When working with your space to design the perfect crane or under the hook apparatus for your unique requirements and challenging business demands, our team can help ensure you are getting the most from your investment, and provide a cohesive and efficient solution, following all OSHA and ANSI regulations.
LOAD TESTING
OSHA requires rated load tests for any new or altered crane. Ace has a fully equipped service department that can help you schedule and perform crane load tests with the results provided as a certificate of proof for your records. Whether you have a large, heavy duty crane requiring the use of massive water weights or a smaller scale crane where test weights will suffice, no load test is too big or too small for Ace Service.
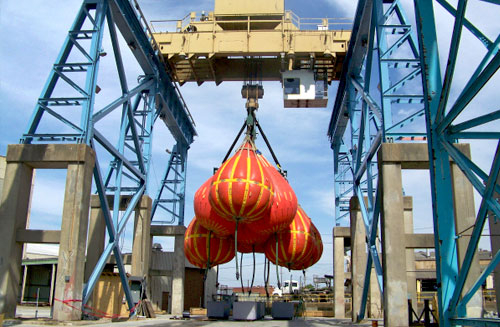
Capacity (Ton): Any amount of weight or tonnage, no limit |
Mount: Either water or test weights, depending on scale of equipment |
Key Benefit: Ensures the total safety of new or altered cranes |
Per OSHA requirement (OSHA 1910.179 (k) Testing), load tests are performed on cranes after new installations or after any modifications or alterations have been made to the lifting equipment, prior to its first use. Trained Ace service technicians perform load tests between 100-125% of the crane’s capacity to ensure the system can handle the maxiumum weight capacity during standard operations. A certificate of proof is provided for you records when completed.
CRANE COMPONENTS
RUNWAYS
A runway is the assembly of rails, girders, brackets and framework on which the crane operates. The crane type will dictate whether the end trucks ride on top of the runway rail or on the bottom flange of the runway beam. Your crane’s runway design and ASCE rail size will determine whether it’s feasible to use the existing structure for any future crane support or the cost associated with increasing its capacity, if necessary. Runways should be installed per CMAA runway specifications and tolerances. Runways that are not installed per CMAA runway specifications or are misaligned due to wear and tear may cause premature wheel wear and other crane and component issues. An engineered runway survey is recommended, if you have abnormal wheel wear, bridge skewing, loud scraping sounds or other indications of a potential runway problem.
TYPES OF RUNWAYS AND RUNWAY COMPONENTS
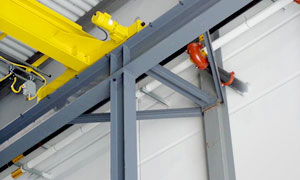
Runway System using Sister Columns and Tied Back to Building
- Building is able to support lateral loads from runway system.
- Our standard tieback is a bolted flexible tieback design vs. rigid tiebacks.
- Flexible tiebacks allow the tie back to flex.
- The runway deflects and vibrates as the crane travels.
- Rigid tieback welds are put under repeated fatigue loading.
- The bolted flexible tieback is highly recommended for larger capacity systems.
- Longitudinal bracing is standard on all of Ace Industries’ crane systems.
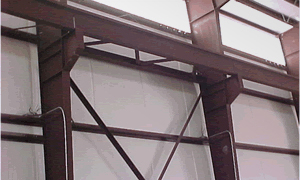
Runway on Haunches
- Haunches or secondary columns mount directly on building columns.
- Building design must be able to support crane loadings.

Free Standing Runway System
- Used if building cannot support any loading and footers may be required.
- Requires more steel to fabricate vs. a system that can be tied back.
- Ace uses moment columns vs. “A” frame columns.
- Moment columns use the foundation to support and stabilize the system.
- No bracing is needed, more steel in the column than a system tied to building.
- A-Frame columns may be less expensive, but take up more space.
- Longitudinal bracing is standard on all Ace crane systems.
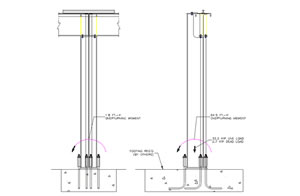
Moment Columns
- Footer takes lateral and longitudinal loads imposed on the system.
- Takes up minimal floor space.
- Larger footer design.
- Increases the cost of the system, but the best choice for columns.

Ceiling Mounted
- Mounted to building trusses or other support structure.
- Longitudinal bracing required on both sides.
- Lateral bracing required-one side only.
- Building and roof truss design may limit options.
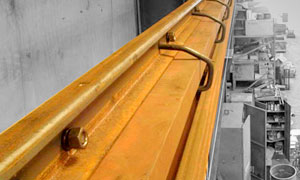
Rail
- Hot rolled steel the crane travels on.
- Subject to very high stresses.
- Ace uses moment columns vs. “A” frame columns.
- Rail size may vary depending system capacity.
- Attachment options: J bolts, weld on and bolt on clips.
END TRUCKS
End trucks ride on the runway rail and move the bridge crane. The two types of end truck designs are the fixed axle and the rotating axle.
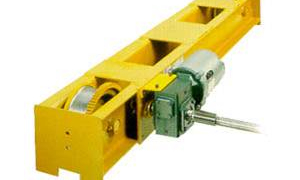
Fixed Axle
- A fixed axle has an exposed gear on the wheel.
- Requires maintenance to keep the exposed gear lubricated.
- Fixed axle end trucks are class C duty cycle.
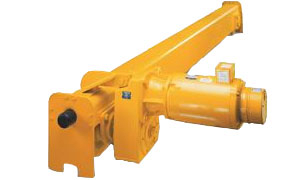
Rotating Axle
- A rotating axle’s wheel is directly driven by the motor through a gear box.
- Requires less maintenance.
- Rotating axle end trucks are class D duty cycle.
- Minimum of 10,000 hours of wheel bearing life
ELECTRIFICATION TYPES
Most hoists and cranes are powered by electricity. Electrification components of hoist and crane systems are relatively simple. There are two circuits in most hoist electrification systems, power and control.
POWER SYSTEMS
The power circuit provides the energy to lift loads and run other motors.

Rigid Bar
- Comes in any length.
- Can be moderately priced to expensive.
- Can handle multiple hoists.
- Can negotiate curves.
Potential Concerns
- Voltage drop on long runs
- Requires hangers every five (5) feet
- Collectors & bar require replacement over time
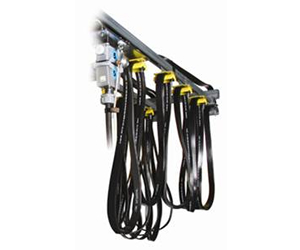
Festoon
- Short length (under 50’)
- Moderately expensive
- Very little maintenance
Potential Concerns
- Long runs put stress on cable
- Large cable requires heavy duty track and trolleys
- Can handle two hoists maximum on one track
- Requires hangers every five (5) feet

Cable Reel
- Short length (under 50’)
- Relatively inexpensive.
- Only a reel hangar is required.
- Can negotiate curves.
Potential Concerns
- Limited on length
- Cable sag
- Reel spring can pull manual trolleys
- Must have slip ring for 360 degree rotation
CONTROL SYSTEMS AND VARIABLE FREQUENCY DRIVES (VFDS)
The control circuitry activates the devices that turn the main motors on and off. The control circuit operates at lower voltage and current than the power or primary circuit.

Pendant Control Stations
Ace offers a wide variety of pendant stations, with 2, 4, 6, 8, 10 and 12 button options in stock, usually available to ship the same day. Pendant control stations can be wired to operate the hoist, trolley or bridge. They’re an economical solution for operating a crane, but most customers prefer a radio remote control system for crane operator safety reasons, as they provide better visibility and freedom from close proximity to a crane. Pendant control stations can function as a secondary back-up control option when a radio remote control is installed for primary use.
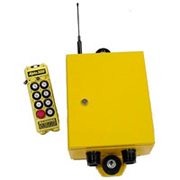
Radio Remote Controls
Ace stocks a variety of radio (wireless) controls. Radio remote controls should always be considered, because they allow the operator freedom from the load and better visibility. A radio remote control system is comprised of two transmitters, a charger unit and a receiver unit. An audible or visual warning device must be installed on a traveling bridge crane, if a radio remote crane control system is installed. The reliability of radio remote controls has increased over the years while the cost associated has decreased.
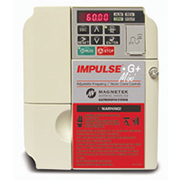
Variable Frequency Drives
A Variable Frequency Drive (VFD) system controls the rotational speed of an alternating current electric motor. VFDs enable the crane operator to better control the load with softer starts and programmable controlled acceleration and deceleration and allows the operator to perform precision load placement and lifting.
POWERED CHAIN HOISTS
Electric chain hoists, simply put, use an electric motor and controller to vertically lift or lower a load. Because they are motorized and have the lifting strength of a machine, they have a high carrying capacity, are efficient, cost-effective, versatile and durable.
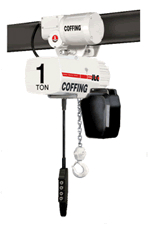
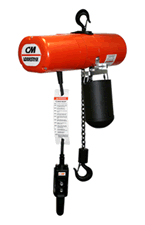


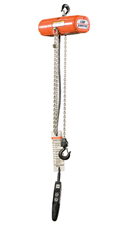

Suspensions
- Hook
- Push or Motor Driven Trolley
Standard Options
- Lift Changes
- Lift (Trolley) Speed
- Two Speed Control
- Voltage
- Chain Container
- Beam Size for Trolleys
Custom Mechanical Options
- Spark Resistance
- Corrosion Resistance
- Weatherproofing
- Food Grade Lubrication
- Mechanical Overload Protection
- Stainless Steel Chain
- Stainless Steel or Bronze Trolley Wheels
- Trolley Safety Lugs (Drop Stops)
- Curved Track Operation
Custom Electrical Options
- Special Control Enclosures
- Mainline Disconnect
- Branch Circuit Fusing
- Thermal Overload Relays
POWERED WIRE ROPE HOISTS
Steel wire ropes are more suitable for very heavy lifting than chains, have a higher strength to weight ratio and can lift up to three times the load. Steel wire ropes are made up of multiple steel wires wound into cables, which are then wound around a central core into the final wire rope. Steel ropes are extremely resistant to corrosion, rust and abrasion and come in a range of sizes and materials.

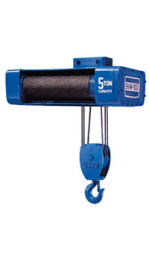


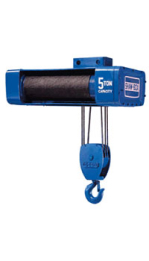
Suspension Type
- Push
- Hand Geared
- Motor Driven
Standard Options
- Lift Changes - Different Drum Sizes
- Lift (Trolley) Speed
- Two Speed Control
- Voltage
- Chain Container
- Beam Size for Trolleys
Custom Mechanical Options
- Curved Track Operation
- Epoxy Paint
- Spark Resistance
- Corrosion Resistance
- Weatherproofing
- Food Grade Lubrication
- Mechanical
- Overload Protection
- Stainless Steel Wire Rope
- Stainless Steel Trolley Wheels
- Trolley Safety Lugs (Drop Stops)
Custom Electrical Options
- Explosion Proof
- Special Control Enclosures
- Mainline Disconnect
- Branch Circuit Fusing, Thermal Overload Relays
- NEMA Rated
- Contactors
- Variable Frequency Drive Control
- Inching Control
- Electronic Overload Protection
- Motor Heaters
- Additional
- Limit Switches