Crane Inspections in Perspective
The combination of timely inspections and a thorough preventative maintenance program are not only required by law but are also essential to the safe, efficient, and cost-effective operation of overhead lifting equipment. Ace Industries’ Certified Crane Care Inspection Program is specifically designed to provide inspections and preventative maintenance guidelines in accordance with all appropriate governing bodies, safety codes, manufacturer’s guidelines, and industry best practices surrounding overhead lifting equipment.
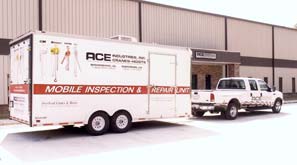
Ace’s Certified Crane Care Inspection Program rigorously follows the guidelines for the construction, maintenance and inspection of Overhead and Gantry Cranes as laid out by the OSHA and ANSI codes. OSHA regulations define requirements for frequent inspections and documented, periodic inspections for Overhead Bridge, Monorails,and Gantry Cranes. All Ace inspectors are trained in the interpretation and application of Occupational Health and Safety Administration (OSHA) Code of Federal Regulations 1910.179, American National Standards Institute (ANSI) B30, and the Crane Manufacturer’s Association of America (CMAA) Specification 78.
Certified Crane Care Inspection Program
Ace Industries, Inc. is unwavering in its commitment to providing the most effective, highest quality, and most valuable services for our customers. Ace’s uncompromising pursuit of excellence is encompassed in the four primary goals of Ace’s Certified Crane Care Inspection Program. The goals of Ace’s program are summarized below:
- Safety
- Industry Best Practices
- Preventative Maintenance
- Compliance - OSHA & ANSI Regulations
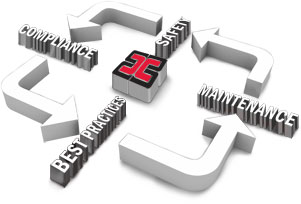
Ace engineered each component of the Certified Crane Care Inspection Program to fuse the elements of safety, industry best practice, preventative maintenance, and compliance into one program. Every element of Ace’s 250+ point inspection is designed to provide appropriate and rapid feedback to our customers. For more information about the goals of Ace’s Certified Crane Care Inspection Program, see the following detailed explanations of Ace’s commitment to its inspection goals.
Safety
Safety is the primary goal of Ace’s inspection program. All Ace inspectors are taught that safety starts first with the individual inspector, follows with Ace’s overall commitment to safety, and concludes with the delivery of Ace’s safety commitment to our customers’ facilities.
Best Practices
As an industry leader in the overhead material handling industry for over 75 years, Ace provides years of expertise, resources, and equipment to all Ace associates to benefit our customers and vendors. Ace maintains a rigorous training and certification program to ensure that all Ace inspectors understand industry best practices for construction and maintenance of overhead material handling equipment. Ace’s training is designed to leverage our years of knowledge and expertise to provide the greatest value for our customers.
Ace’s 250+ point inspection reports are designed to provide a rapid, easy-to-read format for our customers to address preventative maintenance and repair efforts. Ace inspectors understand that preventative maintenance is a key component to any effective inspection program, and our inspectors are trained to make our customers aware of any problems or defects in equipment so our customers may turn maintenance efforts towards enhancements and corrective actions which are vital to the safety and success of their company.
Compliance
Ace’s inspection program is also designed to ensure that our customers’ lifting equipment conforms to all applicable OSHA, ANSI and CMAA regulations regarding safety, construction, and reliability for overhead lifting equipment. All Ace inspectors are trained in the interpretation, application, and understanding of OSHA, ANSI, and CMAA codes. Additionally, Ace’s program is designed to ensure that our customers have the proper documentation for maintenance and inspection as required by law. Ace holds all inspections for our customers in an on-site database that can be accessed whenever needed.
The Inspection Reports
For your convenience, Ace organizes all inspection reports by Ace Industries Equipment ID which is a numeric, sequential numbering system outlined by Ace technicians during inspection.
All inspection reports will be displayed in two sections for easy reference. Section One (1) contains summaries and repair worksheets for each piece of equipment that should be used for rapid-assessment of your equipment. Ace recommends using Section One (1) as the primary reference pages for all review of your equipment. Section Two (2) contains detailed inspection records that can be used for more in depth study of your equipment and any deficiencies found.
Section 1 - Summaries & Repair Worksheet
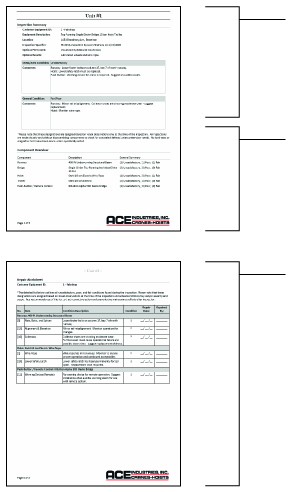
Inspection Summary
General overview of the unit that includes the Equipment ID, Equipment Description, and a high-level summary of any OSHA/ANSI Condition and General Condition found during the inspection.
Component Overview
List of all components (i.e. Runway, Bridge, Hoist, etc) for a piece of equipment with a count of unsatisfactory, fair, and poor conditions found for each component.
Repair Worksheet
A detailed repair list of all unsatisfactory, poor, and fair conditions found during your inspection. This worksheet is subcategorized by each component that makes up an entire piece of equipment. Use this worksheet for a quick overview, consolidated list of all problems, and track maintenance and repair efforts to bring your equipment upto code. If your equipment does not have any problem codes, this sheet will not be included for the piece of equipment.
Section 2 - Detailed Reports
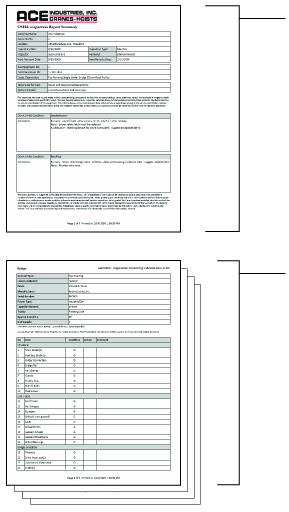
Equipment Details
The Ace legacy equipment overview page. This page provides all the information you are accustomed to seeing on your inspection reports from Ace. Use this page to see a general overview of OSHA/ANSI Conditions and General Conditions of a particular piece of equipment. Additional information such as Equipment ID, Equipment Description, Inspection Date, and Inspector can be found on the Equipment Details page.
Component Details
The original Ace details pages. You can find one page for each component that makes up a piece of equipment (ex. Monorail, Hoist, Trolley, Push-Button, etc.). Use these pages to find specific details such as type, model number, serial number, capacity, voltage, and much more. Additionally, this page shows every item that was inspected on the piece of equipment and the corresponding good, fair, poor, and unsatisfactory conditions.
Conventions Found in the Inspection Reports
The following conventions are used in all inspection reports:
Good: Condition of an item, component, or piece of equipment that requires no special attention at this time.
Fair: Condition of an item, component, or piece of equipment that could possibly cause a breakdown, malfunction, or unsafe condition before the next scheduled periodic inspection.
Poor: Condition of an item, component, or piece of equipment that will likely cause a breakdown, malfunction, or unsafe condition before the next scheduled periodic inspection.
Unsatisfactory: Condition of an item, component, or piece of equipment that should be repaired as soon as possible as it is in violation of OSHA or ANSI standards as they pertain to overhead cranes and hoists or is an immediate danger or safety concern.
Actions Required
Disassembly Required: Condition of an item, component, or piece of equipment that requires disassembly for further evaluation. By marking items with Disassembly Required, Ace recommends planned maintenance and disassembly that does not recommend immediate disassembly unless otherwise noted.
Corrective Action Made: Action was taken during the time of inspection to correct, repair, or modify an existing breakdown, malfunction, or unsafe condition before the inspection was completed. By marking items with Corrective Action Taken, Ace inspectors denote specific actions taken during the time of inspection and note requirements for future repairs, modifications, or monitoring required if applicable.
Emergency Service
Emergency service needs little explanation. We understand the importance of hoisting equipment to our customers and we take the responsibility for emergency service very seriously. We will do everything possible to insure that you are not in an emergency situation for any longer than is absolutely necessary.
Ace will get you up and running quickly. Our strategically located service centers, unequaled factory authorized parts inventories, mobile hydraulic lifts, expert factory trained technicians, and fully equipped trucks make the difference. Our 24 hour 7 day a week emergency parts service and factory authorized technician availability system assures you of round the clock protection.
Experience has taught us that breakdowns often recur unless the failure cause is identified and corrected. Our technicians have been trained to find the cause for the failure and then "put the problem to bed" once and for all time.
Many customers have found that regularly scheduled inspections and load tests by Ace are the best insurance available against breakdowns.
Installations & Modernizations
Ace Industries Inc. has a history of being the service provider of choice for installations and major modernizations. Ace's reputation for innovation and execution is backed by years of field experience, with the support of a robust engineering department. When consulting with our customers, realistic budget estimates that factor “what it will take to do the job right” is one of our primary goals.
Installation and modernization projects vary in size and complexity. Whether a project involves a 1 ton or an 800 Ton, Ace has the technical experience and resources to be the primary consultant of choice. Here is one example of a large modernization project completed on time and within budget.
Ace Industries Awarded Three Large Capacity Crane Modernizations
Ace Industries was awarded three major modernizations in Tennessee designed to improve the crane performance, reliability, availability and safety of the overhead bridge cranes. The modernizations include complete control upgrades, brake replacements, motor refurbishment and various mechanical repairs. The project includes the following cranes which are scheduled to begin production in June 2009.
- 800 Ton Indoor Crane
- 400 Ton Outdoor Crane
- 300 Ton Indoor Crane
Ace Industries also performs removal services for equipment such as the 400 ton outdoor bridge crane pictured below. Ace technicians completed this removal during harsh weather conditions in order to meet the timeline provided by the customer. Throughout the difficult circumstances, safety was never compromised and the project was completed on time and within budget.
Factory Authorized Hoist and Crane Repair Services
Ace Industries is a factory authorized service center and master parts distributor for almost every major hoist, crane, and overhead lifting component manufacturer.
We provide authorized service and parts for:
Budgit
CM
Coffing
CraneMart
Electromotive
Harrington
Ingersoll-Rand
Jet
LiftTech
R&M
Shaw Box
Stahl
Stearns brakes
Wright
and Many Others!
Ace authorized service is distinguished by the experience of our technicians, and the immediate availability of factory authorized parts from our local warehouses.
The manufacturers that have chosen Ace to represent them, read like a who''s who of the best hoist, crane, and overhead lifting accessory companies in the world. These relationships have been formed and strengthened over decades. This insures our customers, who often have equipment from several manufacturers, of the highest quality service, most rapid response, lowest parts price, and one source responsibility for their authorized service and repair needs.
The skill and experience of our factory authorized technicians is unsurpassed. Fifteen years of hoist and crane repair experience is the norm, and many have over 20 years. Ace does not have to, and will not, send two technicians to do a job that requires only one. This assures you of a lasting solution to your service problem at the lowest possible cost.
Each of our strategically located warehouses contains a full stock of crane and hoist parts required to respond to our customer''s needs on a timely basis. This inventory has been developed and improved during our 85 plus years of existence.
When you need factory authorized service call Ace.